Formation of the Solid-Electrolyte-Interphase on Graphite Anodes
A deeper understanding of the solid-electrolyte interphase (SEI) formation process and its influence on the LiB performance and durability is needed. For that, we have coupled standard electrochemical techniques with the on-line electrochemical mass spectrometry to clarify the effect of temperature on the SEI characteristics and their effect on the durability of LiBs containing widespread electrolyte additives.
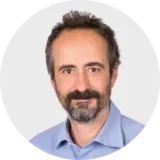
Focus Group Electrochemical Interfaces in Batteries
Dr. Filippo Maglia (BMW Group), Alumnus Rudolf Diesel Industry Fellow | Lennart Reuter (TUM), Doctoral Candidate | Host: Prof. Hubert Gasteiger (TUM)
Major obstacles for battery electric vehicles (BEVs) to be competitive with internal combustion engine ones have been identified as the limited driving range, high cost of the battery system, extended charge period, and capacity fading. Thus, the Focus Group Electrochemical Interfaces in Batteries aims to improve the capability and lifetime of lithium-ion batteries (LiBs). [1]
Most performance indicators of lithium-ion batteries (LiBs), including charge / discharge efficiency, rate capability, and cycle life, heavily depend on the many competing processes that occur at the interphases between the electrodes and the electrolyte. The most investigated interface in LiBs is the so-called solid-electrolyte-interphase, which is the product of electrolyte decomposition occurring at the negative electrode (anode) during the very first operating cycles. [2] Most anode materials (including the most widespread, i.e. graphite) operate in fact outside the voltage stability window of commercially available electrolytes. A general working principle is displayed in Figure 1.
Figure 1
Being permeable towards Li+-ions diffusion but electronically isolating, the SEI acts as a passivating layer allowing normal LiB operation but preventing further electrolyte reduction. Understanding and improving the SEI formation process is of critical relevance to the LiB industry. To yield an effective SEI, commercial battery cells undergo extensive and time-consuming formation procedures directly after cell assembly, comprising multiple voltage holds and current steps at various temperatures. [3]
In more detail, the SEI is a chemically and morphologically complex layer containing inorganic and organic compounds. Most of these compounds are reduction products of the commonly used cyclic, e.g., ethylene carbonate (EC), and linear carbonate-based electrolyte solvents. Linear carbonates such as ethyl methyl carbonate (EMC), dimethyl carbonate (DMC), and diethyl carbonate (DEC) are widely employed in LiB applications due to their low viscosity, high salt solubility, and high conductivity. [4] Additionally, organic electrolyte additives are commonly added to form an SEI layer with increased cycling stability and reduced irreversible capacity loss during the first cycle. [5] Among a variety of additives, vinylene carbonate (VC) is the most prominent.
The decomposition reaction of carbonates, together with the formation of the solid species contained in the SEI, is accompanied by the evolution of gaseous species. The amount, composition, and time of evolution of such gases are indicative of the underlying chemical reactions and can be used to elucidate the effect of electrolyte additives, reveal substantial degradation processes within LiBs, and rationalize optimized formation strategies. [6]
The evolution of gaseous species is typically quantified in-situ by monitoring the cell pressure (e.g., via the so-called Archimedes principle) or by online mass spectrometry. [7] Concerning the latter, an on-line electrochemical mass spectrometer (OEMS) was developed for the application in LiB research and proved to be particularly powerful since it allows a quantitative analysis and the identification of the evolved and consumed gas during the operation of a battery. [8]
However, the application of an OEMS is challenging when the vapor pressure of the electrolyte is high, as it is the case with most LiBs electrolytes due to the presence of highly volatile linear carbonates. At elevated temperatures, in particular a significant share of the gas present in the head-space of the OEMS cell, will consist of electrolyte vapor whose components undergo fragmentation in the mass spectrometer. As a consequence, a large background signal is superimposed on the relevant mass traces related to hydrogen, ethylene, carbon monoxide, oxygen, and carbon dioxide. [9] To mitigate this effect, we developed an elaborate method for signal normalization, a correction for the electrolyte background change, and a precise practice for signal quantification of evolved gas species with commercial electrolytes.
The method allowed us to interpret the temperature-dependent SEI formation for cells containing an additive-free (LP57: 1 M LiPF6 in EC:EMC 3:7wt / wt) and additive-containing (LP572: LP57 + 2wt % VC) electrolyte. For the former, we were able to determine how the formation temperature influences the gas evolution as well as how the bulk of the electrolyte degrades during formation. We were able to conclude that increasing the formation temperature from 25 ° C to 45 ° C significantly increases the overall amount of all relevant gases. More specifically, higher temperatures induce a rapid jump in the amount of the evolved ethylene indicating a change from lithium ethylene dicarbonate (LEDC) to lithium carbonate (Li2CO3) as the primary reduction product of EC in the SEI. Additionally, the trans-esterification of EMC to form DMC and DEC proved to be highly temperature dependent leading to a conversion of approx. 15 vol % EMC at 45 ° C
(summarized in Figure 2).
Figure 2
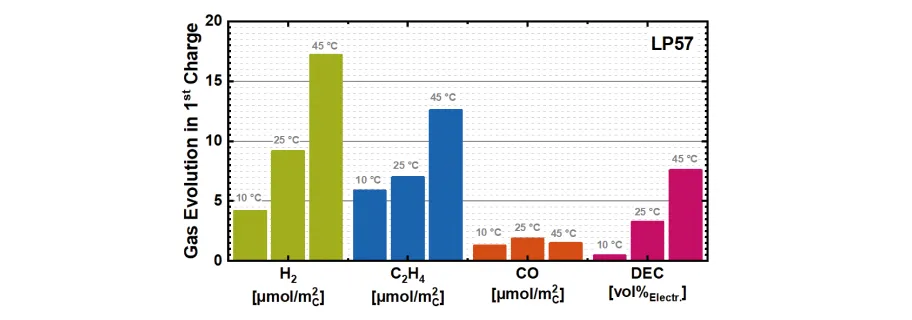
The SEI formation in the presence of the electrolyte additive changes significantly. The reduction of VC initiates at higher reduction potentials compared to alkyl carbonate solvents (e.g., EC), and therefore it is reduced preferentially during the first charge. [10] We compared the formation temperatures in a range between 10-60 ° C by investigating the performance of both full-cells (i.e. graphite anode and a Ni-rich NCM cathode) as well as of graphite / Li half-cells. We could conclude that the formation at 10 and 25 ° C is most favorable due to the lowest initial Li-loss attributed to SEI formation, cell resistance over cycling (see Figure 3 (b)), lowest SEI-related gas evolution during formation, and a very similar capacity fade (see Figure 3 (a)) compared to cells formed at elevated temperatures. Consequently, the formation at lower temperatures is beneficial for a higher energy density of the cell and a higher rate performance.
This understanding will help to rationalize formation conditions in an industrial application and to extend driving ranges as well as optimize charging periods of LiBs in a BEV application.
Figure 3
[1]
Egbue, O. & Long, S. Barriers to widespread adoption of electric vehicles: An analysis of consumer attitudes and perceptions. Energy Policy 48, 717–729 (2012).
[2]
Peled, E. The Electrochemical Behavior of Alkali and Alkaline Earth Metals in Nonaqueous Battery Systems–The Solid Electrolyte Interphase Model. J. Electrochem. Soc. 126, 2047–2051 (1979).
[3]
Miura, T., Cotte, S. & Masanori, K. Lithium-Ion Battery Formation Process 8 (2018).
[4]
Zhang, B. et al. Role of 1,3-propane sultone and vinylene carbonate in solid electrolyte interface formation and gas generation. J. Phys. Chem. C 119, 11337–11348 (2015).
[5]
Taskovic, T. et al. Optimizing Electrolyte Additive Loadings in NMC532 / Graphite Cells: Vinylene Carbonate and Ethylene Sulfate. J. Electrochem. Soc. (2021).
[6]
Jung, R. et al. Oxygen Release and Its Effect on the Cycling Stability of LiNixMnyCozO2 (NMC) Cathode Materials for Li-Ion Batteries. J. Electrochem. Soc. 164, A1361–A1377 (2017); Aiken, C. P. et al. An Apparatus for the Study of In Situ Gas Evolution in Li-Ion Pouch Cells. J. Electrochem. Soc. 161, 1548–1554 (2014); Schreiner, D. et al. Comparative Evaluation of LMR-NCM and NCA Cathode Active Materials in Multilayer Lithium-Ion Pouch Cells: Part I. Production, Electrode Characterization, and Formation. J. Electrochem. Soc. 168, 030507 (2021).
[7]
Aiken, C. P. et al. An Apparatus for the Study of In Situ Gas Evolution in Li-Ion Pouch Cells. J. Electrochem. Soc. 161, 1548–1554 (2014); Metzger, M. et al. Anodic oxidation of conductive carbon and ethylene carbonate in high-voltage Li-Ion batteries quantified by on-line electrochemical mass spectrometry. J. Electrochem. Soc. 162, A1123–A1134 (2015).
[8]
Jung, R. et al. Oxygen Release and Its Effect on the Cycling Stability of LiNixMnyCozO2 (NMC) Cathode Materials for Li-Ion Batteries. J. Electrochem. Soc. 164, A1361–A1377 (2017); Metzger, M. et al. Anodic oxidation of conductive carbon and ethylene carbonate in high-voltage Li-Ion batteries quantified by on-line electrochemical mass spectrometry. J. Electrochem. Soc. 162, A1123–A1134 (2015).
[9]
Strehle, B. et al. The Effect of CO2 on Alkyl Carbonate Trans-Esterification during Formation of Graphite Electrodes in Li-Ion Batteries. J. Electrochem. Soc. 164, A2513–A2526 (2017).
[10]
Zhang, B. et al. Role of 1,3-propane sultone and vinylene carbonate in solid electrolyte interface formation and gas generation. J. Phys. Chem. C 119, 11337–11348 (2015).
Selected publications
-
Strmcnik, D. et al. Electrocatalytic transformation of HF impurity to H2 and LiF in lithium-ion batteries. Nat. Catal. 1, 255–262 (2018).
-
Castelli, I. E. et al. The role of an interface in stabilizing reaction intermediates for hydrogen evolution in aprotic electrolytes. Chem. Sci. 11.15, 3914–3922 (2020).
-
Reuter, L. et al. Temperature-Dependent Gassing Analysis by On-Line Electrochemical Mass Spectrometry of Lithium-Ion Battery Cells with Commercial Electrolytes. Manuscript in preparation.
-
Reuter, L. et al. Temperature Dependent Formation of SEI with Vinylene Carbonate (VC) Electrolyte Additive. Manuscript in preparation.